标准规范下载简介
在线阅读
中华人民共和国国家标准
毛纺织工厂设计规范
Code for design of wool textile factory
GB 51052-2014
主编部门:中国纺织工业联合会
批准部门:中华人民共和国住房和城乡建设部
施行日期:2015年8月1日
中华人民共和国住房和城乡建设部公告
第592号
住房城乡建设部关于发布国家标准《毛纺织工厂设计规范》的公告
本规范由我部标准定额研究所组织中国计划出版社出版发行。
中华人民共和国住房和城乡建设部
2014年12月2日
前言
本规范是根据住房城乡建设部《关于印发<2011年工程建设标准规范制订、修订计划>的通知》(建标[2011]17号)的要求,由中国纺织工业联合会和江苏省纺织工业设计研究院有限公司会同有关单位共同编制完成的。本规范在编制过程中,编制组根据我国毛纺织行业发展现状和行业持续发展的需要,结合毛纺织生产过程的特点,认真总结了我国最近二十年来建设毛纺织工厂的实践经验,吸收了国内毛纺织生产技术的科技成果,广泛征求了有关毛纺织工厂生产、设计、施工等有关专家的意见,经反复讨论、修改,最后经审查定稿。
本规范共分11章和5个附录,主要内容包括:总则,术语,工艺设计,总图布置,建筑结构,给水、排水,采暖通风和空调滤尘,电气,动力,仓储,职业安全卫生等。
本规范中以黑体字标志的条文为强制性条文,必须严格执行。
本规范由住房城乡建设部负责管理和对强制性条文的解释,由中国纺织工业联合会负责日常管理工作,由江苏省纺织工业设计研究院有限公司负责具体技术内容的解释。本规范在实施过程中如发现有需要修订和补充之处,请将意见或建议寄送江苏省纺织工业设计研究院有限公司总师室(地址:江苏省南京市玄武区进香河路31-5号,邮政编码:210008,E-mail:jstd777@126.com),以便今后修订时参考。
本规范主编单位、参编单位、参加单位、主要起草人和主要审查人:
主编单位:中国纺织工业联合会
江苏省纺织工业设计研究院有限公司
参编单位:中国纺织勘察设计协会
上海纺织建筑设计研究院
中国纺织工业设计院
陕西省现代建筑设计研究院
参加单位:宁波雅戈尔毛纺织染整有限公司
主要起草人:陈达俊 邓军 王朝蕾 赵高频 王紫琴 张杰 陈昱 张建伟 陈云霄 周强 林祥程 刘承彬 荆朝晖 赵建生 厚炳煦 徐丽琴 袁依表 秦德兵 宋庆云 李大川 陈洪刚 柳仁南 江雪芳 蔡依群
主要审查人:王耀荣 彭粲云 窦本良 赵燕淑 李熊兆 蒋震华 戴晓培 陈庆丰 饶胤礼
1 总则
1.0.1 为提高毛纺织工厂设计水平,做到技术先进、经济合理、安全可靠、节能环保、清洁生产,制定本规范。
1.0.2 本规范适用于新建、扩建和改建的羊毛、特种动物纤维等的纯纺及与其他纤维混纺的制条、纺纱、织造,以及染整工厂工程的设计。
1.0.3 毛纺织工厂设计,应采用清洁生产工艺和节能、环保、安全生产等技术措施,提高能源利用率和资源的综合利用,且应符合节能、环境影响、安全卫生等评估报告的要求。
1.0.4 毛纺织工厂设计方案应进行技术经济比较择优确定,宜采用经国家有关部门核准推广的新技术、新工艺、新设备和新材料。
1.0.5 分期建设的毛纺织工厂应根据建设规模和发展规划,且应贯彻统筹兼顾、远近期结合、以近期为主的原则。
1.0.6 毛纺织工厂设计应严格执行国家规定的相关行业准入条件,满足节能减排的要求。
1.0.7 毛纺织工厂设计除应符合本规范外,尚应符合国家现行有关标准的规定。
2 术语
2.0.1 选毛 wool sorting
按工业用毛分级标准和产品需要对原毛进行拣选分级的工艺过程。
2.0.2 洗毛 wool scouring
用化学和机械的方法在水或洗涤液中去除原毛所含油脂、汗垢和尘杂的工艺过程。
2.0.3 炭化 carbonizing
将含植物性杂质洗净毛经浸酸、烘焙,使其中的植物性杂质脱水为易碎的炭质,再经机械搓碾、打击、利用风力将炭质与羊毛分离的工艺过程。
2.0.4 毛条制造 top making
把洗净毛加工成精梳毛条的工艺过程。
2.0.5 和毛 wool blending
对不同产地、品种和性能的羊毛或与其他纤维进行合理搭配、均匀混合和添加乳化油的工艺过程。
2.0.6 梳毛 wool carding
将羊毛混料经反复多次的开松梳理、清除各类杂质、充分混合各类原料使之均匀分布,同时使纤维初步伸直、平行排列并制成一定卷装的工艺过程。
2.0.7 针梳 gilling
以机械针板梳理作用将毛条内的纤维理直,使其平行排列并改善毛条均匀度的工艺过程。
2.0.8 复洗 back washing
将毛条充分浸湿、清洗浮色,然后在适当的拉伸张力下烘燥,通过热定型作用消除羊毛卷曲、稳定平伸度的工艺过程。
2.0.9 混条 sliver mixing
将不同颜色、不同性质的毛条,按一定的牵伸倍数和并合根数,制造出混合毛条的工艺过程。
2.0.10 精梳毛纺 worsted spinning
将洗净毛经过以精梳机为核心的多道针梳机加工的精梳制条,再经前纺的多道针梳机、粗纱机反复并合、牵伸、梳理形成粗纱,供细纱机制成毛纱的工艺过程。
2.0.11 粗梳毛纺 woollen spinning
将洗净毛经过粗纺梳毛机的多次开松、混合、梳理,割条、搓捻成粗纱后直接供细纱机制成毛纱的工艺过程。
2.0.12 复精梳 recombing
将已制成的纤维条充分混合后,再经过一次精梳的工艺过程。
2.0.13 条染 top dyeing
对羊毛毛条或其他纤维毛条进行毛球染色的工艺过程。
2.0.14 煮呢 crabbing
毛织物在张力下以平幅状态通过热水处理,以消除呢坯在织造、洗呢、染色等加工中产生的不均匀张力,改善毛织物外观和手感、稳定尺寸、增强弹性的定型加工过程。
2.0.15 缩呢 fulling
在湿热条件和机械作用下,利用羊毛的缩绒性使织物收缩、厚度增加,表面露出一层绒毛来遮盖织物组织,以增加织物美观性,并获得丰满、柔软的手感的加工过程。
2.0.16 刺果起毛 teaseling
利用野生植物刺果的钩刺将毛织物表面均匀地挑出一层绒毛覆盖在表面,使毛织物松厚柔软、保暖性增强、织纹隐蔽的加工过程。
2.0.17 剪毛 shearing
用剪毛机剪短或者剪去织物表面不需要的茸毛的工艺。
2.0.18 蒸呢 decating
为稳定毛织物的尺寸、降低缩水率,使呢面平整、手感柔软、富有弹性、光泽自然,在张力和压力条件下对呢匹进行的蒸汽定型的加工过程。
2.0.19 罐蒸 can decatizing
将呢匹打卷后送进高温高压的汽蒸罐中进行的作用较强烈的蒸呢过程。
2.0.20 整理 finishing
为改善毛纺织制品外观质量、手感和服用性能的加工处理过程。
.
3 工艺设计
3.1 一般规定
3.1.1 毛条厂工艺设计应包括选毛、洗毛和制条及其生产辅助设施设计;精梳毛纺织厂工艺设计应包括条染、复精梳、纺纱、织造、染整及其生产辅助设施设计;粗梳毛纺织厂工艺设计应包括选毛、洗毛、炭化、散毛染色、和毛、梳毛、纺纱、织造、染整及其生产辅助设施设计。
3.1.2 毛纺织工厂的生产类型应根据加工产品使用的原料和产品特征确定。
3.1.3 工艺设计和主机设备应能生产高质量和高附加值的产品,并应符合工艺技术先进、设备性能可靠、适应性强,以及高效、节能的要求。
3.1.4 车间布置除应满足工艺生产的要求,还应满足土建、电气、暖通、空调、动力、给排水,以及其他辅助设施设计的经济合理性的要求,同时应符合消防、环保、节能、安全生产的要求。
3.1.5 公用工程的品质、容量及辅助设施配置应满足工艺生产要求。
3.2 工艺流程
3.2.1 工艺流程应根据加工产品的特征和规格确定。
3.2.2 选毛、洗毛及毛条制造生产工艺流程,可按本规范第A.0.1条确定。
3.2.3 精梳毛纺制品的条染复精梳、纺纱、织造、染整生产工艺流程,可按本规范第A.0.2条确定。
3.2.4 粗梳毛纺制品的选毛、洗毛、炭化、散毛染色、纺纱、织造、染整生产工艺流程,可按本规范第A.0.3条确定。
3.2.5 工艺流程可根据产品要求调整。
3.3 设备选用
3.3.1 设备宜选用标准化、通用化、系列化设备,并应符合下列要求:
1 设备应满足技术成熟的要求,并应适应多品种、小批量生产的要求;
2 设备应满足加工产品的技术要求,并应具有互换互补性;
3 设备应具有易调节、噪声低、动力消耗少、易于维修保养的特点;
4 采用冷却水及有冷凝水排放的设备,应配置冷却水、冷凝水回收利用装置。
3.3.2 间歇式染色设备的选择应满足印染行业准入条件的要求。
3.3.3 后整理宜采用高效、节能、低耗的连续式设备。
3.3.4 设备配台应保证前后工序的产能平衡。
3.3.5 精纺条染和匹染设备、粗纺散毛染色和匹染设备的总加工能力,宜为生产总需要量的130%~160%。
3.3.6 设备配台计算应符合下列要求:
1 前纺、后纺、准备、织造、复精梳、染色和后整理各工序设备配台数的计算,应根据总产量,以及织物规格及细纱机的实际产量和台数确定;
2 主机设备的工艺速度应根据使用原料性质、产品品种和所选用的设备确定;
3 应依据各工序制成率、运转率、生产效率等参数,配置设备台数;
4 主要工艺参数可按本规范附录B选用。
3.4 生产车间布置和设备排列
3.4.1 车间布置应结合厂区总平面布置,车间的原料入口宜靠近原料库,车间的成品出口宜靠近成品库。
3.4.2 各车间的相互位置应保证主要品种的工艺路线合理,半成品和成品的运输路线应便捷,并应避免半制品运输迂回、交叉和逆流。
3.4.3 温湿度要求不同的生产车间和工序,个别散热、散湿和尘土飞毛较大的机台应分开或隔开布置。
3.4.4 车间面积及厂房长度、宽度、高度应合理确定,车间布置应符合现行国家标准《纺织工程设计防火规范》GB 50565的有关规定。
3.4.5 水、蒸汽用量较多的车间应集中布置,废水排放量大的车间宜靠近污水处理系统。
3.4.6 当采用多层厂房时,织布机、梳毛机、洗呢机、煮呢机、染色机、复洗机等设备宜布置在底层。
3.4.7 生产附房宜靠近其服务的车间或机台,并宜布置在主厂房的周边。
3.4.8 生产车间门的位置和尺寸应满足生产管理、产品运输、设备安装及人员疏散的要求,车间外门应采取避免室外气流影响车间温湿度及机台正常运行的措施。
3.4.9 设备布置和排列应符合下列要求:
1 向外排热湿气体的设备宜靠近车间外墙布置;
2 设备排列应满足操作方便、运输通畅、排列整齐及采光的要求;
3 应留有辅助作业和摆放半成品、辅助材料的场地;
4 设备排列间距可按本规范附录C确定。
3.5 工艺要求
3.5.1 工艺用水应符合下列要求:
1 从白毛条到成品精梳毛织物的新鲜水用量不应大于18m³/百米,粗梳毛织物的新鲜水用量应为精梳毛织物的1.15倍。从原毛到洗净毛的新鲜水用量不应大于25m³/t;
2 进设备的给水压力不宜低于0.20MPa;
3 生产用水水质应符合表3.5.1的要求。
表3.5.1 生产用水水质要求
3.5.2 毛纺织厂工艺用蒸汽应符合表3.5.2的要求。
表3.5.2 毛纺织厂工艺用蒸汽要求
2 蒸汽压力、温度可根据设备要求调整。
3.5.3 精纺和粗纺厂车间的温湿度要求可按本规范附录D确定。
3.5.4 进机台的压缩空气压力宜为0.5MPa~0.7MPa。
3.5.5 生产加工过程中烧毛、热定型需要的高温热源,应根据建设地区可供热源选择。
3.6 辅助生产设施
3.6.1 毛条制造、精纺、粗纺可设置下列辅助生产用房:
1 原毛预热室、打土室、和毛油调配室、梳毛磨针室、真空泵房;
2 皮辊室、磨刀室、刺果装排室、筘室、理综室、染料助剂贮存室、染化料调配室;
3 记录室、机物料室、保全保养室、空压机室、空调室、变配电室等。
3.6.2 毛纺织工厂应设置车间试验室及厂部中心试验室,并应配置相应的仪器设备。厂部中心试验室应设置恒温恒湿室,并宜根据试验需要设置相应数量的房间。厂部中心试验室仪器设备可按本规范附录E确定。
3.7 车间运输
3.7.1 车间内的运输工具应根据生产需要选择,部分车间可采用自动运输。
3.7.2 散毛染色、毛条染色半制品的运输,可采用悬挂吊车方式,吊车规格应根据相关设备参数确定。
3.7.3 和毛机与毛仓、毛仓与梳毛仓之间以及洗毛车间洗净毛的运输,宜采用气流管道输送。
3.7.4 多层厂房宜设置客货两用电梯,载重量宜大于2t,数量不宜少于2台。
3.7.5 各车间周转处宜设置地磅或磅秤,车间通道应满足车辆通行和转弯的要求。
.
4 总图布置
4.1 一般规定
4.1.1 总图设计应根据工厂的生产流程、各组成部分的生产特点,在满足各项技术要求的基础上,综合节地、节能、节材、节水及环保、防火、安全卫生等因素确定经济合理的设计方案。
4.1.2 总图设计应符合城镇总体规划的要求,并应做好与邻近工业企业在交通运输、动力设施、综合利用和生活设施等方面的协作。
4.1.3 给排水、供电、供热、道路、消防、环境卫生等厂外配套设施,应结合建厂地区条件,并与相关部门协调后确定方案。
4.1.4 厂址位于湿陷性黄土地区时,除应符合本规范的规定外,还应符合现行国家标准《湿陷性黄土地区建筑规范》GB 50025的有关规定。
4.1.5 总图设计除应符合本规范的规定外,还应符合现行国家标准《工业企业总平面设计规范》GB 50187的有关规定。
4.2 总平面布置
4.2.1 总平面布置应符合生产工艺流程的要求,并应根据各类生产车间和辅助设施的生产特点,结合当地自然条件,确定厂区建(构)筑物、露天堆场、道路、工程管线、绿化等设施的平面及竖向关系。
4.2.2 厂区宜进行合理的功能分区,生产主厂房应布置在地形、地质条件较好的地段,生产联系密切的车间宜紧邻布置,车间内的附属设施应邻近其服务车间,动力供应设施宜靠近生产负荷中心,锅炉房、产生污染源的车间及场所或全厂性废水处理设施等,应位于厂区、生活区全年最小频率风向的上风侧。
4.2.3 厂前区行政办公及生活设施宜集中布置。
4.2.4 厂区内的生产流程组织应合理,人流与货流宜分离,原料及成品的运输路线应便捷。
4.2.5 厂区布置为阶梯式时,相互间运输量大的车间宜布置在同一台阶上。
4.3 竖向设计
4.3.1 竖向设计应与总平面布置同时进行,并应根据厂址自然地形、地质条件、生产工艺、运输方式、防洪、排水、管线敷设及土石方量平衡等因素,进行综合比较后确定各建(构)筑物、道路及场地标高。
4.3.2 厂区内竖向设计宜采用平坡式,在地形复杂地段也可采用阶梯式。
4.3.3 厂区内的标高应与厂区外的场地标高相协调,应避免被洪水、潮水及内涝水淹没。不能满足要求时,应采取防涝、排涝措施,并应符合现行国家标准《防洪标准》GB 50201的有关规定。
4.3.4 厂区出入口的路面标高宜高出厂区外的路面标高。主要建筑物的室内地坪标高应高出室外场地设计标高0.15m~0.30m。
4.4 综合管线
4.4.1 管线敷设方式应根据工艺要求、管线内介质性质、地形地质、生产安全、交通运输、施工检修等因素,经技术经济比较后择优确定。
4.4.2 管线综合布置应与工厂总平面布置、竖向设计和绿化布置统一进行。各管线之间、管线与建(构)筑物之间在平面及竖向上应相互协调、紧凑合理。
4.4.3 管线综合布置应便捷,并应减少交叉。干管应布置在负荷较多的一侧或将管线分类布置在道路两侧。
4.4.4 地下管线管沟不得布置在建(构)筑物的基础压力影响范围内。
4.4.5 管线综合布置应符合现行国家标准《工业企业总平面设计规范》GB 50187的有关规定。
4.5 厂区道路
4.5.1 厂内道路布置应与厂外道路衔接方便,并应满足生产工艺、交通运输、安装检修、管线布置、消防及环境卫生等要求。
4.5.2 厂内道路宜与主要建筑物的外墙平行。主厂房周围宜设环形车道,当设置尽端式道路时,应设回车场、道,型式及各部尺寸应按通过的车型确定。
4.5.3 有货车进出的库房前场地应留有车辆停放和车辆回转用地。
4.5.4 厂区道路宜采用城市型道路,道路路面宽度应根据车辆通行和人行需要确定,并应符合现行国家标准《厂矿道路设计规范》GBJ 22的有关规定。
4.5.5 厂区道路路面标高的确定应与厂区竖向设计相协调,并应满足室外场地及道路的雨水排放要求。
4.5.6 厂区出入口的设置不应少于2个,并宜位于不同方向,位于同一方向时,2个出入口的间距不宜小于50m。
4.6 绿化
4.6.1 厂区绿化应满足项目所在地的规划要求,并应根据工厂特点安排绿化用地。
4.6.2 绿化树种应结合当地自然条件、植物生态习性、抗污性能和苗木来源,按环境保护、工业卫生、厂容景观等要求选择与布置。
4.6.3 厂内道路弯道及交叉口附近的绿化设置,应符合行车视距的有关规定。
4.6.4 厂前区和主要出入口的绿化布置,应具有观赏及美化效果。
4.6.5 树木与建(构)筑物及地下管线的最小间距及绿化布置,应符合现行国家标准《工业企业总平面设计规范》GB 50187和《纺织工业企业环境保护设计规范》GB 50425的有关规定。
4.7 总图技术经济指标
4.7.1 总平面图宜列出下列主要技术经济指标:
1 厂区用地面积(hm²);
2 建筑物、构筑物用地面积(㎡);
3 建筑系数(%);
4 容积率;
5 铁路长度(km);
6 道路及广场用地面积(㎡);
7 绿化用地面积(㎡);
8 绿地率(%);
9 土石方工程量(m³);
10 投资强度(万元/hm²);
11 行政办公及生活服务设施用地面积(hm²);
12 行政办公及生活服务设施用地所占比重(%)。
4.7.2 总图技术经济指标计算方法应符合现行国家标准《工业企业总平面设计规范》GB 50187和《建筑工程建筑面积计算规范》GB/T 50353等的有关规定。
.
5 建筑结构
5.1 一般规定
5.1.1 建筑、结构设计应满足生产工艺的要求,并应满足采光、通风、保温、防水、隔热、防结露、防腐蚀等要求。
5.1.2 建筑物的防火和防爆设计,应符合现行国家标准《纺织工程设计防火规范》GB 50565的有关规定。
5.1.3 建筑、结构设计应采用成熟可靠的新形式、新材料和新技术。
5.1.4 地震区的建筑应选用规则体型,并应符合现行国家标准《建筑抗震设计规范》GB 50011的有关规定。
5.2 生产厂房
5.2.1 生产厂房的建筑、结构形式应根据当地建设条件和其他各种因素,经技术经济比较后确定,可选用单层、多层、气楼式厂房,无窗厂房或其他形式的厂房。非全空调的生产车间应采用自然通风和排气效果良好的建筑形式。
5.2.2 厂房建筑平面和内部空间应满足工艺布置、采光、照明、通风换气等要求,并应满足设备安装操作和相关公用工程设施布置的要求。
5.2.3 厂房围护结构应根据建厂地区的气象条件确定,并应满足建筑物保温、隔热及防结露的要求。湿热车间应设置隔汽层。对单层轻钢结构厂房应加强建筑构造与节点的设计。
5.2.4 厂房的干加工车间地坪应采用耐磨、不起尘砂的面层;洗毛、炭化、条染、湿整等湿车间的地坪应采取防水排水措施;洗毛机、炭化机、洗呢机等设备周围及和毛油调配室地坪应采取防滑措施;纺纱车间的地沟应采取防水措施。
5.2.5 生产车间内有腐蚀性介质的洗毛、炭化、染色、湿整生产车间和染化料调配室、皮辊酸处理间、化验室地沟等的建筑构件表面,应采取建筑防腐蚀措施,且应符合现行国家标准《工业建筑防腐蚀设计规范》GB 50046的有关规定。
5.2.6 有噪声的生产车间应符合现行国家标准《工业企业噪声控制设计规范》GB/T 50087的有关规定。
5.3 辅助用房
5.3.1 生产附属用房宜与厂房紧邻布置。
5.3.2 试验室和检验室宜设置在车间南北侧辅房,成品检验间宜布置在厂房的北面,试验室宜设有恒温室、恒湿室,纺纱试验室宜设置在前、后纺车间的中间位置,化验室应安装排气装置及软水设施,拼毛打样室应在北侧采光,且应靠近染色车间。
5.3.3 原毛预热室、机物料室、染化料储存室等宜靠近厂房外墙布置。
5.3.4 空调室的位置宜靠近负荷中心,进风部位不宜与厕所及散发其他有害气体的房间相邻。空调喷淋水池不应跨越建筑物的变形缝。
5.3.5 空压站、制冷站的位置宜靠近负荷中心,建筑设计应符合现行国家标准《工业企业厂界环境噪声排放标准》GB 12348的有关规定。
5.3.6 变配电室的位置宜靠近用电负荷较大的区域,可建在车间附房内,不应布置在浴室、厕所、水泵房及其他经常积水场所的正下方,且不宜与浴室、厕所、水泵房及其他经常积水场所相贴邻,受条件限制时,应采取防渗漏措施。变配电室不宜跨越建筑物的变形缝。
5.3.7 热力站宜靠近湿加工车间及热负荷中心。
5.3.8 仓库和车间内的辅房宜根据使用要求分别采取通风、防潮、隔热、易于清洁等措施。
5.3.9 羊毛包辐照室应设储源水井及通风系统,平面应为长方形,围护结构应有防辐射措施。
5.4 建筑防火、防爆
5.4.1 当不同火灾危险性的生产工序位于同一防火分区时,该分区的火灾危险性应符合现行国家标准《纺织工程设计防火规范》GB 50565的有关规定。生产厂房的建筑耐火等级不应低于二级。
5.4.2 支撑设备的钢结构,应符合现行国家标准《纺织工程设计防火规范》GB 50565的有关规定。
5.4.3 储存火灾危险性为甲、乙类油料,化学油剂的危险品库与其他建筑物之间的防火间距,应符合现行国家标准《纺织工程设计防火规范》GB 50565的有关规定。
5.4.4 气化室与相邻部位之间应采用防爆墙分隔,其耐火极限不应低于3.0h,隔墙上应设置甲级防火门,外墙应有泄压设施,且应采用不发生火花地面。
5.4.5 烧毛间应采用耐火极限不低于2.50h的不燃烧体隔墙与其他部分隔开。
5.5 结构型式和构造
5.5.1 结构设计应符合下列规定:
1 结构设计应采用新材料、新技术,并应进行多方案比较确定;
2 厂房平面布置及柱网尺寸应根据工艺设备排列及场地自然条件等综合确定;
3 厂房高度除应满足采光与通风要求外,还应满足工艺设备高度、设备安装、检修和操作所需空间,以及设备、管道吊装的安全距离要求。
5.5.2 结构选型应符合下列规定:
1 洗毛、染色、湿整车间可采用带排气井或带气楼的钢筋混凝土结构型式。当采用防腐蚀、防火措施后,也可采用单层轻钢结构型式。
2 选毛、纺纱、织造和干整车间宜采用钢结构,也可采用单层或多层钢筋混凝土框架结构,以及单层钢筋混凝土框架柱钢屋面结构。
5.5.3 荷载取值应符合下列规定:
1 结构自重、施工和检修集中荷载、风荷载、屋面雪荷载和屋面活荷载,应符合现行国家标准《建筑结构荷载规范》GB 50009的有关规定。
2 轻型房屋钢结构的风荷载标准值计算,应符合现行国家标准《钢结构设计规范》GB 50017的有关规定。
3 多层厂房的楼面由设备及运输等产生的局部荷载,应按实际情况计算,也可采用等效均布活荷载代替。楼面等效均布活荷载的确定,应符合现行国家标准《建筑结构荷载规范》GB 50009的有关规定。当差别较大时,应划分区域分别确定。
4 楼层活荷载按工艺设备排列确定时,应符合现行国家标准《建筑结构荷载规范》GB 50009的有关规定。楼面等效均布活荷载应包括按设备实际荷载、生产运行中发生的堆载及产品重量折算的等效荷载和无设备区域的操作荷载之和,无设备区域的操作荷载可按2.0kN/㎡取值。
5 吊挂荷载应按实际重量计算确定。
6 总风道底板活荷载可按1.5kN/㎡取值。
7 沟道盖板的计算活荷载可按10kN/㎡取值。当沟道盖板上直接作用有设备荷载或有运输工具通过时,应按实际荷载经计算确定。
5.5.4 抗震构造设计应符合下列规定:
1 单层门式轻刚架结构的抗震构造要求应符合现行国家标准《建筑抗震设计规范》GB 50011和《钢结构设计规范》GB 50017等的有关规定。
2 钢筋混凝土结构及单层钢筋混凝土框排架钢屋面结构的抗震构造要求,应符合现行国家标准《建筑抗震设计规范》GB 50011、《钢结构设计规范》GB 50017和《混凝土结构设计规范》GB 50010的有关规定。
3 附房宜采用框架结构,抗震措施应按现行国家标准《建筑抗震设计规范》GB 50011的有关规定执行。当附房采用砌体结构并设有总风道时,总风道的抗震措施应符合现行国家标准《建筑抗震设计规范》GB 50011、《构筑物抗震设计规范》GB 50191和《砌体结构设计规范》GB 50003的有关规定。
5.5.5 抗震构造措施应符合下列规定:
1 钢结构厂房的围护墙,当抗震设防烈度不高于7度时,可采用轻型钢墙板,也可采用与柱柔性连接的砌体或底部为砌体、上部为轻型钢墙板;当抗震设防烈度为8度及以上时,应采用压型钢板墙体或轻质墙板。
2 钢结构厂房屋面的隔热保温应采用非燃烧体材料。压型钢板下设有玻璃纤维毡或矿棉毡防潮层时,应采取纤维增强措施。
3 钢筋混凝土结构厂房的非承重墙体宜采用轻质墙体材料。
5.5.6 地基处理应综合场地地质、水文地质、冻土深度、地下沟道管线、相邻建(构)筑物和基础荷重等影响。工艺设备基础的不均匀沉降差应小于工艺设备要求的允许值。
.
6 给水、排水
6.1 一般规定
6.1.1 给水排水设计应符合节约水资源、一水多用的原则,并应满足生产、生活和消防的要求。
6.1.2 室外给水排水管道的平面布置与埋深,应根据地形、地质、冰冻深度、总平面布置、给水排水管道、管道材质、施工条件等因素确定。
6.1.3 给水排水管道管材的选择,应根据使用性质、防火要求、抗震要求及当地条件因地制宜选用,并应符合产品标准的要求。
6.1.4 工厂应提高水的重复利用率,控制新鲜水用量。
6.1.5 给水排水管道不得穿过设备基础,必须穿越时,应采取保护措施并与有关专业协商处理。给水排水管道不应穿过建筑物的伸缩缝和沉降缝,必须穿过时,应采取相应的防护措施。
6.1.6 湿陷性黄土地区的给水排水管道布置,应符合现行国家标准《湿陷性黄土地区建筑规范》GB 50025的有关规定。
6.2 水源与水处理
6.2.1 水源选择应根据当地水源情况、城镇与工业企业规划、供水规模、水质及水压要求等条件经经济比较后确定。
6.2.2 水源选择应符合下列规定:
1 水量、水质应满足生产、生活要求;
2 以地表水为水源的设计枯水流量的年保证率宜为90%~97%。
3 采用城镇自来水为水源时,严禁与工厂自备水源的供水管道直接连接。
6.2.3 水源水质无法直接满足生产、生活要求时,应采取水处理措施。水处理设施和工艺应根据原水水质与生产、生活对水质的要求确定。
6.3 水量、水质、水压
6.3.1 给水用水量应根据工厂工艺用水量、软化水用水量、空调用水量、生活用水量、浇洒道路和绿化用水量、水景用水量、汽车冲洗用水量、管网漏失水量及未预见水量、消防用水量等确定,并应符合下列规定:
1 工艺用水量、软化用水量应根据生产工艺确定,小时变化系数宜为1.4~2.0;
2 空调用水补水量应按空调系统的循环水量确定;
3 生活用水量、浇洒道路和绿化用水量、水景用水量、汽车冲洗用水量,应按现行国家标准《建筑给水排水设计规范》GB 50015的有关规定执行;
4 管网漏失水量及未预见水量可按最高日用水量的10%~15%计算;
5 设有自备给水净化站时,应计算水站自用水量,自用水量应根据原水水质、处理工艺和构筑物类型等因素计算确定,可采用设计水量的5%~10%;
6 消防用水量及水压、供水延续时间等,应符合国家现行有关消防标准的规定。
6.3.2 给水水压应根据生产、生活、消防用水最不利点压力及管网损失等通过计算确定。工艺机台用水压力应根据机台技术参数确定。
6.3.3 工厂用水水质应符合下列规定:
1 生活用水水质应符合现行国家标准《生活饮用水卫生标准》GB 5749的有关规定;
2 锅炉用水水质应符合现行国家标准《工业锅炉水质》GB/T 1576的有关规定;
3 杂用水水质应符合国家现行标准《污水再生利用工程设计规范》GB 50335和《纺织染整工业回用水水质》FZ/T 01107等的有关规定;
4 洗毛和染整用水水质应根据产品种类和质量、染色工艺、设备状况等确定。
6.4 给水系统和管道敷设
6.4.1 给水系统设计应符合下列规定:
1 给水系统设计宜利用城镇给水管网的水压直接供水。不满足要求时,应设置贮水池和加压设施,并应满足卫生、安全、经济、节能的要求。
2 给水系统设计应综合利用水资源,并应充分利用再生水、雨水等非传统水源,宜实行分质供水;宜采用循环和重复利用给水系统。当采用梯级用水、循环用水、再生水、雨水回用时,应做好水量平衡。
3 热水供水系统应根据使用要求、耗热量、用水点分布情况及热源条件单独设置。热源宜利用工业余热、废热、地热和太阳能。
6.4.2 给水管道的管材与敷设应符合下列规定:
1 室外埋地给水管宜采用塑料给水管,可采用有衬里的铸铁给水管、经可靠防腐处理的钢管等。室内给水管宜采用塑料给水管,可采用塑料和金属复合管、不锈钢管、经可靠防腐处理的钢管等。
2 利用城镇给水管网水压且引入管无防回流设施时。向锅炉、热水机组、水加热器、气压水罐等有压或密闭容器注水的进水管上必须设置倒流防止器。
3 厂区总进水管、车间生产进水管和冷却塔补充水总管上应设置水表等计量设施;各工段或主要用水设备处宜设置水表等计量设施。
4 室内给水管道宜沿墙明敷,并应与工艺系统等其他管道统一敷设。给水管与电缆桥架或封闭式母线槽上下平行敷设时,给水管应布置在电缆桥架或封闭式母线槽的下方,净距不应小于0.4m。
5 给水管道不应穿越变配电房、电梯机房、电脑打样室等房间。
6 敷设在有可能结冻的房间、管架、管沟等处的给水管应采取防冻措施。当给水管结露对生产、生活产生影响时,管道应采取防结露措施。
7 给水管道不得敷设在风道、排水沟内。
6.5 消防给水系统
6.5.1 室内外消防给水系统的设置,应符合现行国家标准《建筑设计防火规范》GB 50016、《纺织工程设计防火规范》GB 50565和《自动喷水灭火系统设计规范》GB 50084的有关规定。
6.5.2 灭火器的配置应符合现行国家标准《建筑灭火器配置设计规范》GB 50140的有关规定。
6.6 排水系统和管道敷设
6.6.1 排水量应符合下列规定:
1 生产排水量应以生产用水量为依据,并应区分生产废水、清洁废水的排水量,生产废水的小时变化系数宜为1.5~3.0;
2 生活排水量、雨水排水量的确定,应符合现行国家标准《建筑给水排水设计规范》GB 50015的有关规定。
6.6.2 排水系统应符合下列规定:
1 应采用生产、生活排水与雨水分流的排水系统,宜按质分类、清浊分流、合理划分;
2 洗毛废水应单独分流,染整废水和清洁废水宜分流,也可采用合并的排水系统;
3 食堂含油污水应经隔油池后进入生活污水管;
4 机修含油污水和水温超过40℃的设备排水应经预处理后进入污水处理站;
5 雨水回收利用时可按现行国家标准《建筑与小区雨水利用工程技术规范》GB 50400的有关规定执行;
6 各类废水在排入受纳水体或管网前,废水排放应符合现行国家标准《纺织染整工业水污染物排放标准》GB 4287和地方有关标准的规定。
6.6.3 排水管道的管材与敷设应符合下列规定:
1 室外排水管道宜采用埋地排水塑料管,有特殊要求时,应采用符合相关要求的排水管。室内排水管道宜采用建筑排水塑料管或柔性接口机制排水铸铁管。当连续排水温度大于40℃时,应采用耐热排水管。
2 车间内工艺排水形式可根据生产工艺要求采用管道或排水沟排放。当排水沟采用暗沟排放时,宜在设备排出口、三叉口及转弯处设置活动盖板,并宜每隔3跨~5跨设置伸顶通气管。工艺冷却水宜采用管道排放。
3 当废水中夹带纤维或有大块物体时,应在排出口处采取拦截措施。
4 排放腐蚀性废水时,管道或排水沟应采取防腐措施。
5 当室内管道布置于推车、搬运车经过的位置时,应采取防护措施。
6 排水管道不得敷设在对生产工艺或卫生有特殊要求的生产厂房,以及贵重商品仓库、配电室、变压器室内。
6.7 废水预处理与回用
6.7.1 对有提取羊毛脂价值的洗毛废水应先回收羊毛脂。提取羊毛脂后的洗毛废水宜经预处理后,再与其他废水混合进入后续处理工艺。
6.7.2 生产系统的洁净冷却水、直流水应加以收集、集中、处理后回用。生产废水回用应符合印染行业准入条件,回用水水质应符合现行行业标准《纺织染整工业回用水水质》FZ/T 01107的有关规定。
6.7.3 高温热排水宜实施热能回收。
6.7.4 废水处理与回用应符合现行国家标准《纺织工业企业环境保护设计规范》GB 50425的有关规定。
6.7.5 各类回用水管严禁与生活饮用水管直接连接。
.
7 采暖通风和空调滤尘
7.1 一般规定
7.1.1 采暖通风与空调滤尘设计应符合现行国家标准《采暖通风与空气调节设计规范》GB 50019的有关规定。
7.1.2 采暖通风和空调滤尘设计应满足生产,以及技术先进、经济合理、保护环境和职业安全卫生的要求,并通过综合技术经济比较确定。
7.1.3 空调通风系统消防设计应符合现行国家标准《纺织工程设计防火规范》GB 50565的有关规定。
7.1.4 室外空气的设计计算参数应采用当地气象部门提供的相关资料,并应符合现行国家标准《采暖通风与空气调节设计规范》GB 50019的有关规定。
7.1.5 毛纺织车间室内空气计算温湿度应满足生产工艺要求,温湿度参数可按本规范附录D执行。
7.1.6 车间试验室温湿度参数应按工艺要求确定。温带地区的温度宜为22℃±2℃,相对湿度宜为65%±3%,亚热带地区工厂中心试验室标准大气温度宜为27℃±3℃,相对湿度宜为65%±3%。
7.2 采暖
7.2.1 全年日平均温度稳定低于5℃的天数不小于90d的地区,当生产工艺对温度有要求,或房间经常有人员停留时,房间应设置供暖设施,并宜采用集中供暖。
7.2.2 采暖方式应根据厂区热源条件、工厂建设规模,经技术经济比较确定,并应符合下列规定:
1 宜利用生产过程中产生的余热、废热;
2 生产车间采暖热媒宜采用高温热水,当蒸汽作为工厂主热源时,可采用低压蒸汽作热媒,凝结水应回收;
3 设有通风系统的车间,冬季宜结合通风系统采用热风供暖。
7.2.3 采暖系统管道设计应符合下列规定:
1 生产、空调、采暖及生活用汽宜为各自独立的管路系统;
2 采暖管道应计算热膨胀,当自然补偿不能满足热膨胀要求时,应设置热补偿器;
3 采暖管道经过非采暖及有冻胀危险区域时,应采取保温措施;
4 采暖管道材质、管道敷设方式、热媒的流速等,应符合现行国家标准《采暖通风与空气调节设计规范》GB 50019的有关规定。
7.2.4 洗毛、湿整等相对湿度较大的生产车间,散发腐蚀性气体或有腐蚀性液体外溅的场所,散热器及采暖管道应采取防腐蚀措施。
7.2.5 当散热器表面温度较高可能引发烫伤事故,或散热器周围经常有重物经过有撞击可能时,应采取防烫伤、防撞击保护措施。
7.2.6 散发粉尘或防尘要求较高的区域,应采用易于清扫的散热器。
7.3 通风
7.3.1 设有全面空调系统的车间,新风补给量应符合国家现行有关工业企业设计卫生标准的规定,车间应保持正压。
7.3.2 非全面空调的车间通风宜采用自然通风,不满足要求时,应采用自然与机械联合通风,也可采用机械通风,通风量应满足工艺和职业卫生要求。
7.3.3 采用机械通风的车间,气流组织应有利于热湿气体的排放,通风区域应进行风量平衡计算。选毛、打土、烧毛、染色等散发粉尘、有异味的工段,应保持车间负压,不应使气流流向较清洁的房间。
7.3.4 生产过程中散发高温高湿的设备宜采用局部排风,且应采取防结露措施。
7.3.5 风机的设计工况效率不应低于风机最高效率的90%。
7.3.6 不同型号、不同性能的风机不宜串联或并联使用。
7.3.7 通风管道内的设计风速可按表7.3.7确定。
表7.3.7 通风管道内的设计风速(m/s)
风管类别 | 干管 | 支管 |
钢板及非金属风管 | 2~8 | 6~14 |
砖及混凝土风道 | 2~6 | 4~12 |
7.4 空气调节
7.4.1 生产车间的空调负荷计算应符合下列规定:
1 空调区域围护结构的传热量可采用逐时计算法,并应取计算综合最大值。
2 工艺设备机器发热量可按下式计算:
式中:Q——机器发热量(kW·h);
N——电动设备的安装功率(kW);
n——机器台数(台);
k1——安装系数(利用系数),电动机最大实耗功率与安装功率之比;
k2——同期使用系数;
k3——电动机负荷系数,每小时平均实耗功率与设计最大实耗功率之比;
α——热迁移系数,宜采用实测资料。
3 厂房围护结构传热系数k应根据全面空调车间温湿度要求和室外气象条件确定。在节约能耗和防止结露的条件下,根据不同地区的气象条件,围护结构传热系数宜采用表7.4.1的要求。
表7.4.1 围护结构传热系数k[W/(㎡·K)]
屋面 | 总风道顶板、天沟 | 内墙 | 外墙 |
≤0.35 | 0.40~0.60 | 0.90~1.20 | 0.45~1.50 |
4 生产车间和附房中容易结露和产生冷桥的部位应做防结露验算,并应采取防结露措施。
7.4.2 空气调节系统的设置应符合下列规定:
1 车间空调系统应根据生产工序和温湿度要求划分,同一空调室不宜服务不同防火分区;
2 车间气流组织应有利于温湿度的均匀分布,并应减少能耗、防止二次扬尘。
7.4.3 空气调节设备的选择及空调室的布置,应符合下列规定:
1 毛纺织车间空调空气处理方式应采用喷淋洗涤室。喷淋室的喷淋排数、喷嘴密度应根据喷淋室的热工计算确定;水泵水量及扬程应满足喷淋室的热工计算要求。
2 空调室宜分别设置送风机和回风机,风机的风量宜大于计算值的5%~10%,风机的风压宜大于计算值的10%~15%。
3 吸入式空调室宜用于以降温去湿为主的区域,常年以加湿为主的空调室宜采用以喷雾风机为主的压入式。
4 喷淋室经过自动水过滤器过滤后的水可循环使用或排放。
5 空调室设备应选用技术先进、高效节能、质量可靠的产品,并应便于操作和维修。
6 空调室宜采用饱和蒸汽作为空气加热和加湿的热源。
7.4.4 空调室的布置应符合下列要求:
1 空调室的位置应满足工艺设备布置的要求,并应与相关专业协调;
2 空调室的面积和层高应满足设备安装、操作、测试和维修的要求;
3 空调室应设置补充水和清洗水水源,空调室排水应单独设置,室内排水管与室外排水管相接的管段上水封高度不应小于该处的负压;
4 建筑外墙调节窗的底面与室外地坪的高差不宜小于0.8m,车间回风调节窗底面与车间地坪的高差不宜小于0.5m。
7.4.5 空调送回风管道布置应符合下列要求:
1 采用等截面土建总风道时,高度宜便于操作,总风道应做保温及防渗水处理,紧邻房间应做防结露验算。
2 吊装风管宜采用镀锌薄钢板或其他轻质材料,其主辅材均应符合消防要求。
3 地沟风道内壁应光滑、防潮、不漏风,并应按需设置检查孔、集水井。
4 空气调节系统的控制风速可按表7.4.5选用。
表7.4.5 空气调节系统的控制风速(m/s)
7.5 滤尘
7.5.1 滤尘系统设计应满足生产工艺和职业安全卫生要求。车间内空气的含尘浓度应达到国家现行有关工作场所有害因素职业接触限值的规定。车间的防尘设计应符合现行国家标准《纺织工业企业职业安全卫生设计规范》GB 50477的有关规定。
7.5.2 滤尘机房宜与空调室相邻布置,滤尘器宜按生产线设置。
7.5.3 滤尘器和滤料应根据滤尘风量和集尘量选择。排尘风机宜选择防缠绕叶片。
7.5.4 滤尘器应采用连续过滤集尘、连续压实排除的组合滤尘设备,严禁采用沉降室除尘。
7.5.5 滤尘管道不宜穿越不同的防火分区,经济风速宜为10m/s~14m/s。滤尘管道应设置检查孔。
.
8 电 气
8.1 一般规定
8.1.1 供配电系统设计应满足生产要求,并应符合安全可靠、技术先进、操作方便和经济合理的要求。
8.1.2 供配电设计宜使用技术先进、性能可靠、节能环保的电气设备和材料。
8.2 负荷分级
8.2.1 用电负荷分级除应符合本规范的规定外,尚应符合现行国家标准《供配电系统设计规范》GB 50052的规定。
8.2.2 毛纺织工厂的一般用电应为三级负荷。
8.2.3 毛纺织工厂下列场所的消防用电应按二级负荷供电:
1 室外消防用水量大于30L/s的厂房、仓库;
2 室外消防用水量大于35L/s的可燃材料堆场。
8.2.4 除本规范第8.2.3条规定的建筑物和堆场等的消防用电外,其他可采用三级负荷供电。
8.2.5 毛纺织工厂二级负荷的供电宜由两回线路供电,也可采用一回线路供电外加自备应急电源方式。在负荷较小或地区供电条件困难时,二级负荷可由一回6kV及以上专用的架空线路供电。
8.3 供配电
8.3.1 电源电压等级与供电回路数,应根据工厂建设规模、用电容量、供电条件和工艺要求等因素确定。
8.3.2 毛纺织工厂的供电电压宜采用10kV,低压配电电压应采用220V/380V。
8.3.3 车间变电所应符合下列规定:
1 车间变电所应根据建设规模和负荷分布设置一个或数个车间变电所;
2 车间变电所宜设置在车间附房,并宜靠近负荷中心;
3 相邻两个车间变电所之间宜设置低压联络。
8.3.4 变压器的选择和布置应符合下列规定:
1 变压器台数应根据负荷特点和经济运行等因素确定;
2 应选用节能环保型、低损耗、低噪音的三相变压器,变压器的接线组别宜选用D,yn11;
3 不带可燃性油的高、低压配电装置和非油浸的电力变压器可设置在同一房间内,应具有符合IP3X防护等级外壳的不带可燃性油的高、低压配电装置和非油浸的电力变压器,当环境允许时,可互相靠近布置在车间内;
4 油浸式变压器应安装在单独的变压器室内,并应符合现行国家标准《20kV及以下变电所设计规范》GB 50053的有关规定。
8.3.5 20kV及以下变电所的设计除应符合本规范的规定外,还应符合现行国家标准《20kV及以下变电所设计规范》GB 50053的有关规定。
8.3.6 低压配电系统设计除应符合本规范的规定外,还应符合现行国家标准《低压配电设计规范》GB 50054的有关规定。
8.4 照明
8.4.1 毛纺织工厂的车间照明宜采用一般照明,选毛、穿综穿筘、验布和修布等工段可采用混合照明。车间一般照明应采用高光效光源、高效灯具和节能器材;混合照明可根据用途及环境采用适用的光源。和毛仓应采用密封性能优良的防火专用灯具。
8.4.2 灯具布置应根据建筑结构、灯具型式和生产要求确定。
8.4.3 主要生产车间或场所的一般照明标准值应符合表8.4.3的规定。
表8.4.3 主要生产车间或场所的一般照明标准值
8.4.4 车间作业区内的一般照明照度均匀度不应小于0.7,作业面邻近周围的照度均匀度不应小于0.5。
8.4.5 毛纺织工厂消防应急照明和消防疏散指示标志的设置,应符合现行国家标准《建筑设计防火规范》GB 50016的有关规定。
8.4.6 照明配电系统应采用三相四线制,并应采取防频闪措施。车间照明应按工序、工段或操作工车位设照明配电箱。
8.5 火灾自动报警系统
8.5.1 火灾自动报警系统的设置应符合现行国家标准《纺织工程设计防火规范》GB 50565的有关规定。
8.5.2 火灾自动报警系统的设计应符合现行国家标准《纺织工程设计防火规范》GB 50565和《火灾自动报警系统设计规范》GB 50116的有关规定。
8.6 防雷与接地
8.6.1 毛纺织工厂的建筑物、构筑物应根据防雷类别划分采取相应的防雷措施,且应符合现行国家标准《建筑物防雷设计规范》GB 50057的有关规定。
8.6.2 毛纺织工厂的户外燃料油、润滑油储罐应采取相应的防雷措施,且应符合现行国家标准《石油库设计规范》GB 50074的有关规定。
8.6.3 化工原料罐、可燃气体罐应采取相应的防雷措施,且应符合现行国家标准《石油化工企业设计防火规范》GB 50160的有关规定。
8.6.4 存在静电引燃、引爆危险的场所应设置静电防护措施,且应符合现行国家标准《防止静电事故通用导则》GB 12158等的有关规定。
8.6.5 毛纺织工厂的低压配电系统接地型式宜采用TN系统,接地电阻值不应大于4Ω。不同接地系统共用接地装置时,接地电阻值应按最小值要求。
8.6.6 接地保护除应符合本规范外,还应符合现行国家标准《系统接地的型式及安全技术要求》GB 14050的有关规定。
8.7 无功补偿与谐波治理
8.7.1 毛纺织工厂的供电系统应设无功功率集中或分级补偿装置,补偿后的功率因数不应低于0.9。供电部门另有要求时,应符合供电部门的有关规定。
8.7.2 谐波治理宜根据建设项目的实际情况和供电部门的要求采取治理措施。
.
9 动 力
9.1 一般规定
9.1.1 毛纺织工厂的用热负荷应包括生产工艺、空调、采暖和生活用热。
9.1.2 热源的供应应根据所在区域的供热规划确定。当热源不能由区域热电厂、区域锅炉房或其他企业的锅炉房供应时,应自设锅炉房。
9.1.3 锅炉房的设计应符合现行国家标准《锅炉房设计规范》GB 50041的有关规定,并应与安全生产、经济效益和环境保护相结合。锅炉燃料的选用应做到合理利用能源和节约能源。
9.1.4 蒸汽、燃气、压缩空气、导热油、冷冻水等介质,应设置计量装置。
9.2 蒸汽供热系统
9.2.1 毛纺织工厂的最大热负荷计算应按生产、空调、采暖、生活和锅炉自用热负荷之和乘以同时使用系数并计算管网损失后得出。生产用热和生活用热宜分别设置。
9.2.2 当采用城市(区)热电厂集中供热,且供热参数不满足生产要求时,应设置减压减温装置,且宜有一套备用。
9.2.3 生产用汽应在热力站集中控制,各主要车间宜单独敷设干管。
9.2.4 管道设计流量应根据热负荷计算确定,热负荷应包括近期发展的需要量。
9.3 蒸汽凝结水回收和利用
9.3.1 使用蒸汽间接加热而产生的凝结水,应回收利用。
9.3.2 高压和低压凝结水系统应分别敷设。空调、采暖凝结水应与生产凝结水分别敷设。
9.3.3 蒸汽凝结水的回收方式和设备,应根据用汽特点和条件、管道敷设方式等综合分析后确定。
9.3.4 蒸汽凝结水的回收系统宜与工艺生产热废水的热回收系统相结合。
9.4 导热油供热系统
9.4.1 毛纺织工厂使用热载体加热炉为高温热源时,加热炉选型应根据工艺设备用热参数、热负荷量及当地燃料条件确定,且宜设置备台。
9.4.2 热载体加热炉房的位置宜靠近热负荷中心。使用同种燃料的热载体加热炉房宜与蒸汽锅炉房布置在同一区域,且宜合用辅助设施。
9.4.3 导热油供热系统设计应选用导热油在炉管中的流速、导热油炉进出口油温的温差,并应采取防止导热油氧化及油温过高的措施。
9.4.4 当建有油罐区时,油罐区的设计应符合现行国家标准《纺织工程设计防火规范》GB 50565的有关规定。
9.5 燃气
9.5.1 毛纺织工厂的燃气管道设计应符合现行国家标准《城镇燃气设计规范》GB 50028及《工业企业煤气安全规程》GB 6222的有关规定。
9.5.2 进车间的燃气管道宜架空敷设。
9.6 压缩空气
9.6.1 压缩空气站的设计容量应依据工艺提供的设备用气压力、用气量、用气品质要求,计入同时使用系数、管道系统漏损系数后计算确定。
9.6.2 压缩空气站的设计应符合现行国家标准《压缩空气站设计规范》GB 50029的有关规定。
9.7 制冷
9.7.1 制冷站宜靠近负荷中心。
9.7.2 制冷机的选择应综合工厂建设规模、使用特征、空气调节冷负荷,以及当地能源结构、政策、价格和环境保护等因素确定。
9.7.3 制冷设备的单台容量及台数选择,应适应空气调节的冷负荷特性。
9.7.4 制冷系统管道应采取保冷措施。
9.7.5 制冷站的设计应符合现行国家标准《采暖通风与空气调节设计规范》GB 50019的有关规定。
9.8 管道敷设
9.8.1 厂区热力管道应根据热负荷分布确定,并应结合空压管、燃气管、给水排水管等设置管架、管沟。
9.8.2 车间内蒸汽管道的布置应便于安装、操作和检修,管道宜沿墙和柱敷设,应满足装设仪表的要求,不应妨碍门、窗的启闭与室内采光。
9.8.3 架空管道在不妨碍交通的地段可采用低支架敷设,通过人行通道地段宜采用中支架敷设,在车辆通行地段应采用高支架敷设。
9.8.4 热力管道可与重油管、压力不大于1.6MPa(表压)的压缩空气管、给水管敷设在同一地沟内。
9.8.5 热力管道热膨胀的补偿应利用管道的自然补偿,不满足要求时,应设置补偿器。
9.8.6 管道设计应采取防止表面结露的措施。
.
10 仓 储
10.1 一般规定
10.1.1 物资储备应满足保证生产、加快周转、防止损失的要求,并应合理确定仓库的面积。10.1.2 仓库布置应方便生产和运输,宜靠近使用部门。
10.1.3 库区和库内货物的装卸运输应提高机械化程度。
10.2 原料库、成品库
10.2.1 原毛的储存周期可根据原料市场供应确定,在供应充足、采购方便时,原毛储存周期可按2个月~3个月计;全部由本厂储存时,可按6个月~9个月计。选后毛储存周期可按1个月~2个月计。原毛库及选后毛库可根据当地情况,设置仓库、棚库或露天堆场。10.2.2 粗纺厂用的洗净毛、炭化毛及化纤散纤维的储存周期可按3个月~4个月计。洗净毛、炭化毛库可根据当地情况,设置仓库或棚库。化纤散纤维宜采用仓库储存。
10.2.3 精纺厂用的毛条、化纤条,储存周期可按1个月~3个月计,宜采用仓库储存。
10.2.4 洗净毛、炭化毛及呢绒等成品的储存周期可按1个月~3个月计,宜采用仓库储存。
10.2.5 原料库和成品库的建筑面积可根据荷重法按下式计算:
式中:S——仓库面积(㎡);
Q——日存储量(kg);
T——储存周期(d);
q——单位面积储存能力(kg/㎡);
f——面积利用系数,可取0.5~0.6。
10.2.6 仓库堆卸设备可采用移动式堆包机、单梁吊车或装卸板等设施。多层仓库可采用电梯垂直运输。成品布包底层应设置垫木。
10.3 染化料库及助剂的储存
10.3.1 染化料和助剂的储存周期可按1个月计。10.3.2 桶装或袋装的染化料和助剂的储存能力可按300kg/㎡~500kg/㎡计,面积利用系数宜为0.5~0.6。
10.4 危险品库
10.4.1 危险品库内应分隔成若干间,并应将各类物品分开堆放。10.4.2 危险品库应防止太阳直晒,库内应保持干燥、阴凉、通风,并应配置消防设施。
10.5 机物料、机配件库
10.5.1 机物料和机配件的储存周期可根据企业规模和市场供应确定。10.5.2 机物料和机配件库内各种小件物品的储存可采用层式货架,人工存取的货架高度不宜超过2.5m。
10.6 其他仓库
10.6.1 色毛球、粗纱、细纱、筒纱、坯布等中间库,应根据企业规模、生产计划、品种安排等,按方便生产、就近安排的原则布置。10.6.2 润滑油库可根据工厂规模设置,面积可为15㎡~30㎡。
11 职业安全卫生
11.0.1 职业安全卫生设计应贯彻“以人为本、安全第一、防治结合、预防为主”的指导方针。
11.0.2 工作场所的危险和有害因素应完整调查分析。治理和防范措施应做到技术先进、经济合理、安全适用。
11.0.3 职业安全卫生设计除应符合本规范的规定外,尚应符合现行国家标准《纺织工业企业职业安全卫生设计规范》GB 50477的有关规定。
11.0.4 原毛应采取消毒措施。当采用钴60辐射法消毒时,辐射室应采取安全防护措施。钴60的使用、贮存、运输、装卸,以及监督和管理设计,应按现行国家标准《电离辐射防护与辐射源安全基本标准》GB 18871的有关规定执行。
11.0.5 选毛车间应与洗毛车间分隔。打土间应单独设置,并应设置除尘装置。磨皮辊机应设置独立的吸尘装置。
11.0.6 选毛工作台除尘吸风口宜设置水平吸尘。洗毛车间采用洗毛废水处理闭路循环系统时,应设置控制循环使用时间和洗液含菌量的大、小循环系统,洗毛车间应采取通风排湿措施。
11.0.7 蒸刷机、剪毛机、钢丝起毛机、起剪联合机等设备应设置局部除尘装置。炭化机除杂部分应设置除尘装置。
11.0.8 梳毛机宜采用真空抄针、真空吸尘技术。揩油渍工作台和称量室应设置排气装置。修焊针室应对铅烟进行处理,室内空气中的铅烟含量应低于0.03mg/m³。
11.0.9 梳毛车间、纺纱车间和织造车间,以及除尘室和空压站等的噪声超过职业卫生标准的规定值时,应采取降噪措施。
11.0.10 和毛油调制室,洗毛、复洗机,洗呢机,洗绒机,染线机,脱水机等设备周围地面、操作台,应采取防滑措施。
11.0.11 选毛和打土工序应设淋浴室,浴室内不应设浴池。
附录A 工艺流程
A.0.1 选毛、洗毛及毛条制造生产工艺流程,应符合下列要求:
1 羊毛应为原毛→选毛(手拣)→(打土)→洗毛→洗净毛;
2 羊绒应为原绒→选绒→打土→洗绒→复选→开松混和→分梳→打包→无毛绒;
3 毛条制造应为洗净毛→和毛→梳毛→毛条头道针梳→毛条二道针梳→毛条三道针梳→精梳机→条筒针梳→末道针梳。
A.0.2 精梳毛纺制品的生产工艺流程,应符合下列要求:
1 条染复精梳工艺流程应为(松球)→压球→染色→脱水→复洗→混条→针梳(前一)→针梳(前二)→精梳机→针梳(后一)→针梳(后二)→色毛条;
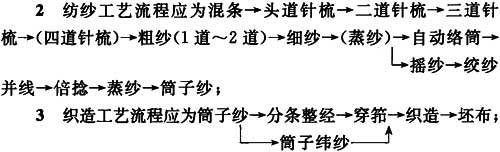
4 染整工艺流程应为坯布→检验→生修→(烧毛→揩油渍)→洗呢(洗缩)→煮呢→吸水→(染色→开幅)→煮呢→吸水→烘呢(定型)→中检→熟修→蒸刷→剪呢→给湿→烫光→蒸呢→预缩→成检→卷呢→包装→入库;
5 匹染产品可不经过条染复精梳工序,复精梳车间的针梳道数可根据产品要求增减,单纱产品可不经过并线、倍捻,染整工艺流程可根据染整工艺、工序、设备进行调整。
A.0.3 粗梳毛纺制品的生产工艺流程,应符合下列要求:
1 选毛、洗毛、炭化、染色工艺流程应为原毛→选毛→洗毛→炭化→染色→脱水→烘干→染色毛。

3 染整工艺流程应符合下列要求:
1)纹面织物应为坯布→检验→生修→(缩呢)→洗呢→脱水→(染色→脱水)→烘干→中检→熟修→剪毛→蒸刷→烫光→蒸呢(罐蒸)→成检→折卷→包装→入库;
2)呢面织物应为坯布→检验→生修→洗呢→缩呢→脱水→(染色→脱水)→(缩呢→洗呢)→脱水→烘干→中检→熟修→(起毛)→剪毛→蒸刷→烫光→蒸呢(罐蒸)→成检→折卷→包装→入库;
3)立绒织物应为坯布→检验→生修→洗呢→缩呢→脱水→(染色→脱水)→烘干→中检→熟修→起剪联合→成检→折卷(卷呢)→入库;
4)顺毛织物应为坯呢→检验→生修→洗呢→缩呢→脱水→烘干→中检→熟修→起剪联合→湿刷→浸轧→刺果起毛→烘干→刷、剪多次→烫光→成检→折卷(卷呢)→入库。
4 匹染产品可不经过散毛染色工序。染整工艺流程可根据染整工艺、工序、设备进行调整。
附录B 主要工艺参数
B.0.1 洗毛、选毛和毛条制造工艺参数可按表B.0.1选用。
表B.0.1 洗毛、选毛和毛条制造工艺参数
B.0.2 精梳毛纺制品条染复精梳工艺参数可按表B.0.2选用。
表B.0.2 精梳毛纺制品条染复精梳工艺参数
B.0.3 精梳毛纺制品纺纱织造工艺参数可按表B.0.3选用。
表B.0.3 精梳毛纺制品纺纱织造工艺参数
B.0.4 精梳毛纺制品染整工艺参数可按表B.0.4选用。
表B.0.4 精梳毛纺制品染整工艺参数
B.0.5 粗梳毛纺制品炭化纺纱织造工艺参数可按表B.0.5选用。
表B.0.5 粗梳毛纺制品炭化纺纱织造工艺参数
注:1 工艺参数以目前国内生产厂使用较多的国产和进口设备为参考,设计时应根据实际选用的设备确定。
2 粗梳毛纺制品染整工艺参数可按精梳毛纺制品染整相应工序执行。
.
附录C 主要设备排列间距
C.1 精梳毛纺
C.1.1 毛条及纺织设备排列间距可按表C.1.1确定。
表C.1.1 毛条及纺织设备排列间距
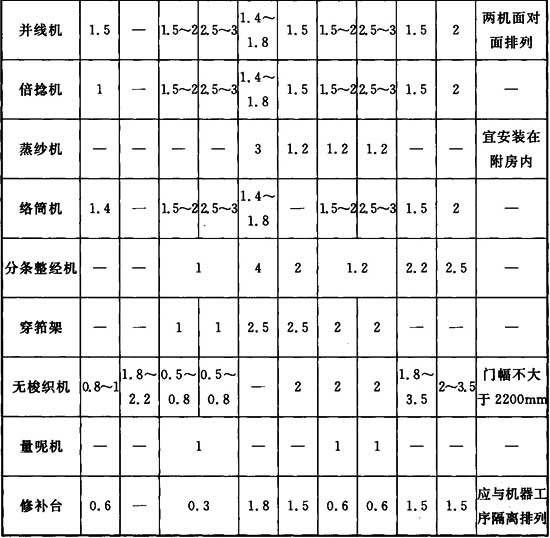
C.1.2 染整设备排列间距可按表C.1.2确定。
表C.1.2 染整设备排列间距
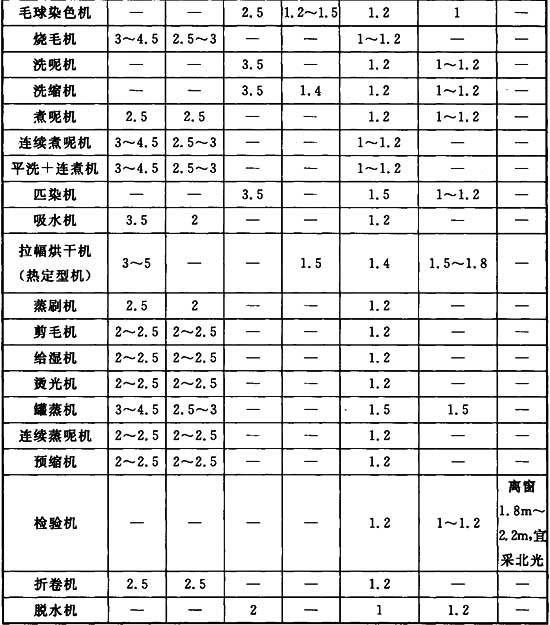
2 输出产品处为挡车弄,喂入处为后车,有主电动机的一侧为车头,其对侧为车尾。
3 细纱机、自动络筒机、并线机、倍捻机、挡车弄离柱净距0.5m。
4 车间不同设备之间应根据需要确定半制品的周转空间。
5 烫光机压力带检修侧与墙的距离不应小于2.2m。
C.2 粗梳毛纺
C.2.1 纺织设备排列间距可按表C.2.1确定。
表C.2.1 纺织设备排列间距
C.2.2 染整设备排列间距可按表C.2.2确定。
表C.2.2 染整设备排列间距
附录D 车间温湿度参数
D.0.1 精纺厂车间温湿度参数可按表D.0.1确定。
表D.0.1 精纺厂车间温湿度参数
D.0.2 粗纺厂车间温湿度参数可按表D.0.2确定。
表D.0.2 粗纺厂车间温湿度参数
注:分梳间主要为羊绒分梳。
附录E 试验室仪器设备
E.0.1 试验室仪器设备可按表E.0.1确定。
表E.0.1 毛纺织厂中心试验室仪器表
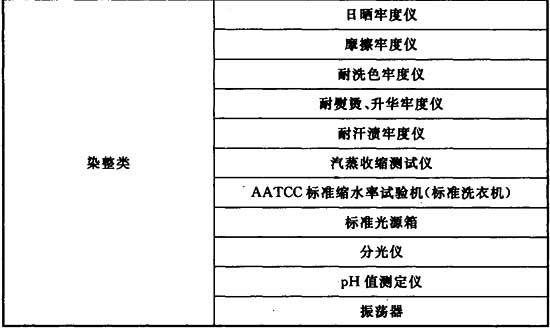
注:1 本表仪器选型以国产为主,企业可根据自身需要选择,仪器宜根据企业检测项目增减或合并。
2 配置OFDA4000型羊毛细度长度仪时,可不配置激光细度仪和ALMETER长度仪。
3 本表不含车间试验室的仪器。
本规范用词说明
1 为便于在执行本规范条文时区别对待,对要求严格程度不同的用词说明如下:
1)表示很严格,非这样做不可的:
正面词采用“必须”,反面词采用“严禁”;
2)表示严格,在正常情况下均应这样做的:
正面词采用“应”,反面词采用“不应”或“不得”;
3)表示允许稍有选择,在条件许可时首先应这样做的:
正面词采用“宜”,反面词采用“不宜”;
4)表示有选择,在一定条件下可以这样做的,采用“可”。
2 条文中指明应按其他有关标准执行的写法为:“应符合……的规定”或“应按……执行”。
引用标准名录
《砌体结构设计规范》GB 50003
《建筑结构荷载规范》GB 50009
《混凝土结构设计规范》GB 50010
《建筑抗震设计规范》GB 50011
《建筑给水排水设计规范》GB 50015
《建筑设计防火规范》GB 50016
《钢结构设计规范》GB 50017
《采暖通风与空气调节设计规范》GB 50019
《厂矿道路设计规范》GBJ 22
《湿陷性黄土地区建筑规范》GB 50025
《城镇燃气设计规范》GB 50028
《压缩空气站设计规范》GB 50029
《建筑照明设计标准》GB 50034
《锅炉房设计规范》GB 50041
《工业建筑防腐蚀设计规范》GB 50046
《供配电系统设计规范》GB 50052
《20kV及以下变电所设计规范》GB 50053
《低压配电设计规范》GB 50054
《建筑物防雷设计规范》GB 50057
《石油库设计规范》GB 50074
《自动喷水灭火系统设计规范》GB 50084
《工业企业噪声控制设计规范》GB/T 50087
《火灾自动报警系统设计规范》GB 50116
《建筑灭火器配置设计规范》GB 50140
《石油化工企业设计防火规范》GB 50160
《工业企业总平面设计规范》GB 50187
《构筑物抗震设计规范》GB 50191
《防洪标准》GB 50201
《污水再生利用工程设计规范》GB 50335
《建筑工程建筑面积计算规范》GB/T 50353
《建筑与小区雨水利用工程技术规范》GB 50400
《纺织工业企业环境保护设计规范》GB 50425
《纺织工业企业职业安全卫生设计规范》GB 50477
《纺织工程设计防火规范》GB 50565
《工业锅炉水质》GB/T 1576
《纺织染整工业水污染物排放标准》GB 4287
《生活饮用水卫生标准》GB 5749
《工业企业煤气安全规程》GB 6222
《防止静电事故通用导则》GB 12158
《工业企业厂界环境噪声排放标准》GB 12348
《系统接地的型式及安全技术要求》GB 14050
《电离辐射防护与辐射源安全基本标准》GB 18871
《纺织染整工业回用水水质》FZ/T 01107